SWD8028 polyaspartic anticorrosion coating
Features and benefits
* high solids low density, with good leveling, the coating film is tough, dense, full light and bright colors
* excellent adhesive strength, good compatible with polyurethane, epoxy and other coating film.
* high hardness, good scratch resistance and stain resistance
* excellent abrasion resistance, impact resistance
* excellent anticorrosion property, resist to acid, alkali, salt and others.
* no discoloration, UV resistance, no yellowing, no powdering, aging resistance, with excellent weather resistance and gloss and color retention property
* can be applied directly to the surface of metal surface (DTM)
* this product is environmentally friendly and contains no benzene solvents and lead compounds

Product information
Item | A component | B component |
Appearance | light yellow liquid | Color adjustable |
Specific gravity(g/m³) | 1.04 | 1.50 |
Viscosity (cps)@25℃ | 40-60 | 100-200 |
Solid content (%) | 58 | 90 |
Mix ratio (by weight) | 1 | 1 |
Surface dry time (h) | 1 | |
Pot life (h)@25℃ | 1 | |
Theoretical coverage (DFT) | 0.15kg/㎡ film thickness 100μm |
Typical physical properties
Item | Test standard | Results |
Pencil hardness | H | |
Adhesive strength(Mpa)metal base | HG/T 3831-2006 | 9.3 |
Adhesive strength(Mpa)concrete base | HG/T 3831-2006 | 2.8 |
Impermeability | 2.1Mpa | |
Bending test (cylindrical shaft) | ≤1mm | |
Abrasion resistance (750g/500r) mg | HG/T 3831-2006 | 5 |
Impact resistance kg·cm | GB/T 1732 | 50 |
Anti-aging, accelerated aging 1000h | GB/T14522-1993 | Loss of light<1, chalking <1 |
Chemical resistance
Acid resistance 40%H2SO4 or 10%HCI, 240h | no rust, no bubbles, no peel off |
Alkali resistance 40%NaOH, 240h | no rust, no bubbles, no peel off |
Salt resistance 60g/L, 240h | no rust, no bubbles, no peel off |
Salt spray resistance 1000h | no rust, no bubbles, no peel off |
Oil resistance, engine oil 240h | no rust, no bubbles, no peel off |
Water resistance, 48h | No bubbles, no wrinkled,
no color-changing, no peel off |
(Note: The above chemical resistant property is obtained according to the GB/T9274-1988 test method, for reference only. Pay attention to the influence of ventilation, splash and spillage. Independent immersion testing is recommended if requires other specific data.) |

Application instructions
Hand brush, roller
Air spray, with air pressure 0.3-0.5Mpa
Airless spray, with spray pressure 15-20Mpa
Recommend dft: 150-300μm
Recoating interval: min 1h, max 24h
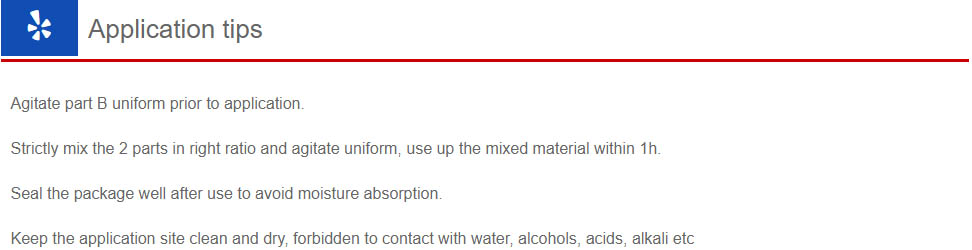
Product cure time
Substrate temperature | Surface dry time | Foot traffic | Solid dry time |
+10℃ | 2h | 24h | 7d |
+20℃ | 1.5h | 8h | 7d |
+30℃ | 1h | 6h | 7d |
Note: the curing time is different with environment condition especially when temperature and relative humidity changes.
Shelf life
Storage temperature of environment: 5-35℃
* shelf life is from the manufacturing date and sealed condition
Part A: 10 months Part B: 10 months
* keep the package drum well sealed.
* store in cool and ventilated place, avoid sunshine exposure.
Package: part A: 25kg/barrel, part B: 25kg/barrel.
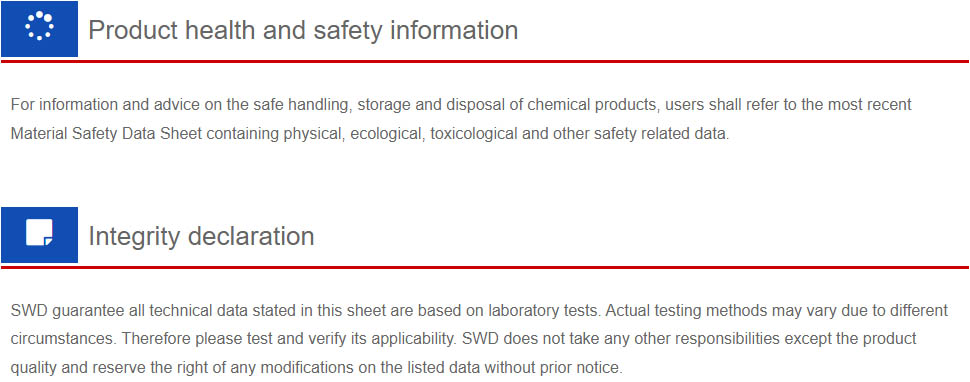